Understanding the Role of Injection Mold Manufacturers in Modern Manufacturing
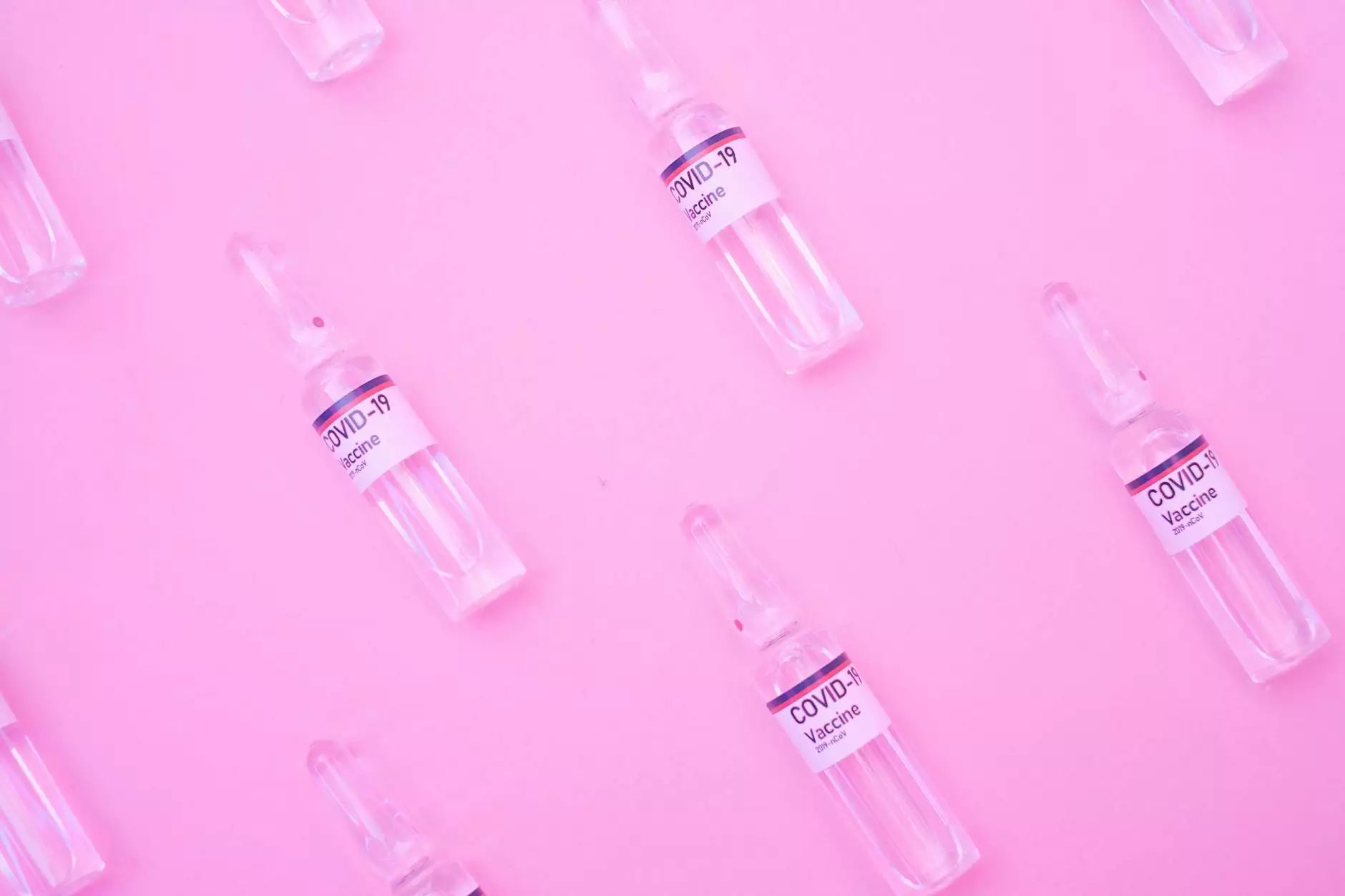
The realm of manufacturing continues to evolve, with specialized industries like injection molding shaping the production of countless products. Within this dynamic landscape, injection mold manufacturers play a pivotal role. They contribute not only to the efficiency of production but also to the innovation of product design.
What is Injection Molding?
Injection molding is a manufacturing process used for producing parts by injecting molten material into a mold. This technique is widely utilized for creating plastic parts but can also involve metals, ceramics, and glass. The process allows for high precision and reproducibility, making it essential in various industries including automotive, consumer goods, and medical devices.
Key Advantages of Using Injection Mold Manufacturers
Engaging with professional injection mold manufacturers provides numerous advantages, including:
- Cost Efficiency: Although the upfront costs of designing and producing molds can be significant, the mass production of parts leads to lower per-unit costs over time.
- Quality Consistency: Injection molding ensures that every part produced meets stringent quality standards and precise specifications.
- Complex Shapes: The technology allows for the production of intricate designs that would be difficult or impossible with other methods.
- Material Versatility: Manufacturers can utilize a wide range of materials, offering flexibility in product design and end-use application.
The Injection Molding Process
The process of injection molding involves several critical steps:
- Material Preparation: The raw material, typically plastic pellets, is fed into a hopper and heated until it reaches a molten state.
- Injection: The molten material is injected under high pressure into a mold that defines the part's shape.
- Cooling: The material is allowed to cool and solidify within the mold, taking on its shape.
- Ejection: Once cooled, the molded part is ejected from the mold, and any excess material is trimmed away.
Challenges Faced by Injection Mold Manufacturers
While injection molding is a highly effective process, injection mold manufacturers do encounter a range of challenges:
- High Initial Costs: The cost of mold design and production can be substantial, which may deter small businesses from utilizing this technology.
- Complex Design Requirements: Designing molds that can produce the desired part without defects requires expertise and precision.
- Material Limitations: Not all materials are suited for injection molding, which can limit choices in product design.
- Sustainability Concerns: The environmental impact of plastic use is becoming a focal point for manufacturers, prompting a shift toward sustainable practices.
The Importance of Choosing the Right Injection Mold Manufacturer
Choosing the right injection mold manufacturer is critical for the success of your project. Factors to consider include:
- Experience and Expertise: Select manufacturers with a proven track record and experience in your specific industry.
- Technological Capabilities: Ensure that the manufacturer has access to the latest technology and equipment to produce high-quality molds.
- Quality Assurance Processes: A robust quality assurance framework is essential to guarantee that the finished products meet industry standards.
- Flexibility: Look for manufacturers willing to adapt their processes to meet your unique requirements.
Future Trends in Injection Molding
As the world of manufacturing continues to innovate, several trends are emerging in the realm of injection molding:
- Advance Materials: The development of new materials, including bio-based and recycled plastics, is becoming increasingly popular.
- Smart Manufacturing: Automation and the Internet of Things (IoT) are streamlining production processes, enhancing efficiency, and reducing costs.
- Sustainability: Manufacturers are striving to implement eco-friendly practices to reduce waste and lower carbon footprints.
- Customization: The demand for customized products is on the rise, pushing manufacturers to offer more diverse options.
Conclusion
The significance of injection mold manufacturers in shaping the future of manufacturing cannot be understated. By embracing advanced technologies and sustainable practices, these manufacturers are poised to lead the industry into a new era of efficiency and innovation. As businesses continue to seek out high-quality, cost-effective solutions, the role of injection molding will only grow in importance, making it a crucial area of focus for future developments.
The journey of collaboration with skilled injection mold manufacturers is vital for achieving production excellence. Companies looking to thrive in their respective markets must align themselves with those who understand the intricacies of this transformative manufacturing method.