High Precision Injection Moulding: A Revolution in Metal Fabrication
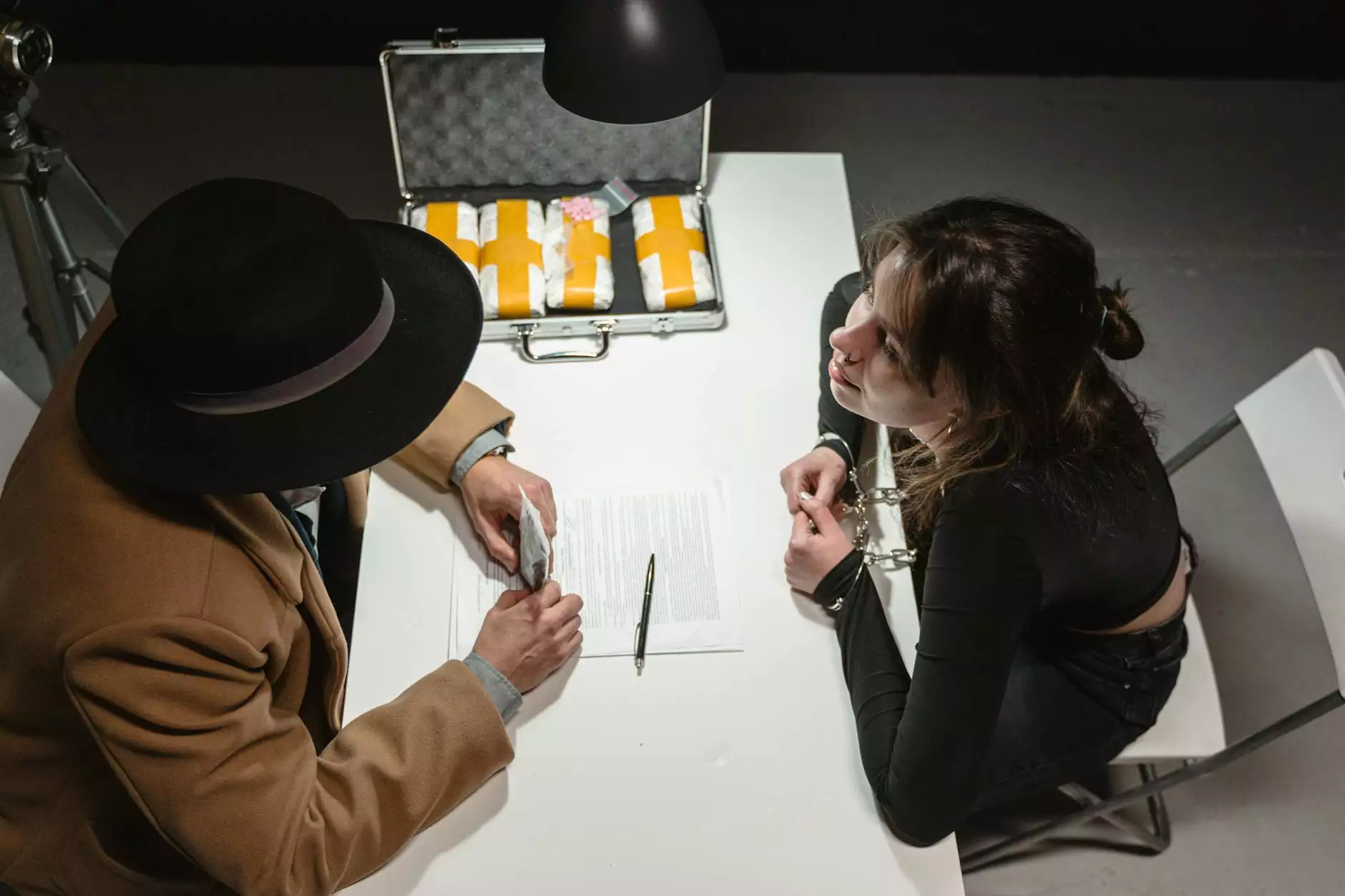
The landscape of manufacturing is continually evolving, and in this transformation, high precision injection moulding has emerged as a pivotal technique that businesses must embrace. As a metal fabricator, understanding this process can mean the difference between being on the cutting edge or falling behind competitors. This article dives deep into high precision injection moulding, exploring its benefits, applications, and why it is essential for modern manufacturing.
What is High Precision Injection Moulding?
High precision injection moulding is a manufacturing process used to create parts by injecting molten material into a mould. This technique is extensively employed in various industries, including automotive, aerospace, electronics, and medical. The precision aspect refers to the ability to produce parts with very tight tolerances, ensuring consistent quality and performance.
Benefits of High Precision Injection Moulding
Adopting high precision injection moulding can offer multiple advantages, such as:
- Enhanced Precision: The ability to produce components with minimal variations increases the reliability of the final product.
- Cost Efficiency: High-volume production reduces the cost per unit, leading to significant savings for businesses.
- Material Versatility: A wide range of materials can be used, including thermoplastics and thermosetting plastics, catering to various industry needs.
- Complex Geometries: Designers can create intricate shapes that are challenging or impossible with other manufacturing methods.
- Reduced Waste: The process generates less scrap compared to traditional machining methods, supporting sustainable manufacturing practices.
Applications of High Precision Injection Moulding
High precision injection moulding finds applications across various industries, where precision and quality are paramount:
- Automotive: Components such as dashboards, trims, and housings require high precision and durability.
- Aerospace: Safety-critical parts need to meet stringent regulations, which high precision moulding can fulfill.
- Electronics: Cases and components for consumer electronics demand tight tolerances to ensure functionality.
- Medical Devices: High precision is crucial for manufacturing devices and components that meet healthcare standards.
- Consumer Goods: Products ranging from household items to toys benefit from the aesthetics and durability made possible through high precision moulding.
How High Precision Injection Moulding Works
The process of high precision injection moulding can be broken down into several key steps:
- Material Preparation: Raw plastic or metal is prepared and heated to a molten state.
- Injection: The molten material is injected into a pre-designed mould under high pressure.
- Cooling: The injected material cools and solidifies to form the desired part.
- Demoulding: Once solidified, the part is carefully removed from the mould.
- Finishing: Additional processes may include trimming, surface finishing, or painting to enhance the product quality.
Importance of Precision in Metal Fabrication
In metal fabrication, precision is not just a luxury; it is a necessity. Poor precision can lead to:
- Increased Costs: Errors in production can result in material waste and increased labor costs.
- Product Failures: Components that do not meet exact specifications can lead to product malfunctions, affecting brand reputation.
- Regulatory Issues: Certain industries, like aerospace and medical, have strict regulations that require exact specifications.
Choosing the Right High Precision Injection Moulding Partner
With many providers available, selecting the right high precision injection moulding partner is crucial for your business success. Consider the following factors:
Experience and Expertise
Evaluate their experience in the industry. A partner with a proven track record will understand the nuances of high precision injection moulding and how to overcome challenges effectively.
Technology and Equipment
Ensure they use the latest technology and high-quality equipment to deliver precision results. Advanced machinery often leads to better quality and efficiency.
Quality Assurance Practices
A strong quality assurance program is essential. Look for partners who adhere to international quality standards, as this reflects their commitment to precision and reliability.
Customer Service
Excellent communication and customer service can make a significant difference. Your partner should be willing to work closely with you through every step of the process.
Future Trends in High Precision Injection Moulding
As technology continues to advance, the field of high precision injection moulding is also evolving. Some upcoming trends that could shape the future include:
- Automation: Increased automation in the injection moulding process can enhance efficiency and reduce human error.
- Advanced Materials: The use of composite materials and new polymers can lead to lighter and stronger components.
- Sustainability: More focus on sustainable practices, including the use of recycled materials and energy-efficient processes.
- 3D Printing Integration: Combining traditional injection moulding with 3D printing capabilities to create even more complex parts and designs.
Conclusion
In summary, high precision injection moulding is a crucial technique in the metal fabrication landscape, offering numerous benefits and applications across various industries. As businesses look to improve efficiency, reduce costs, and deliver high-quality products, adopting this innovative process is no longer optional but essential. By understanding the intricacies of high precision injection moulding and selecting the right partners, metal fabricators like those at deepmould.net can position themselves for success in an ever-competitive marketplace.