Understanding Polyurethane Coated Webbing: The Future of Durable Materials
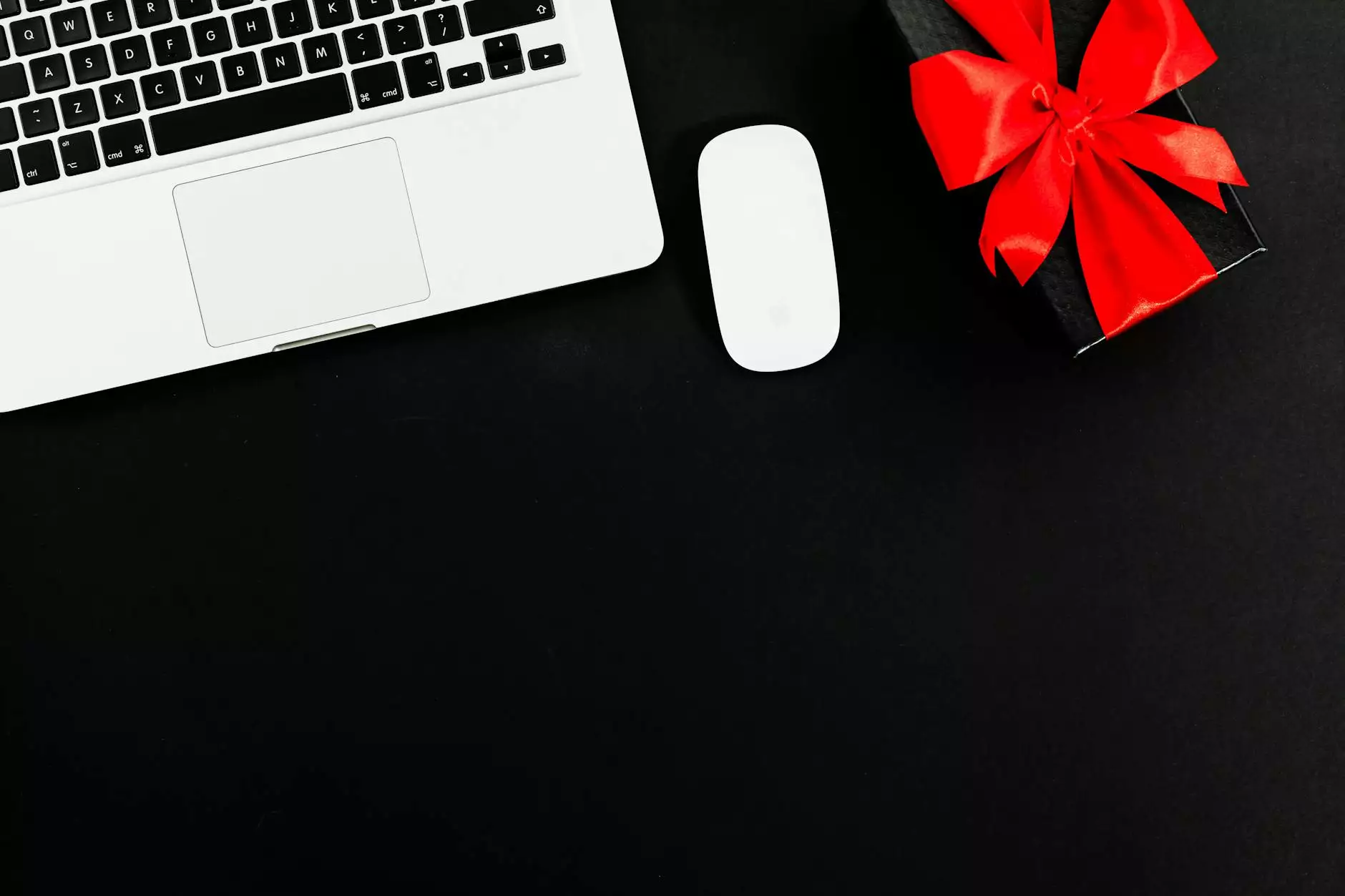
Polyurethane coated webbing is emerging as a transformative material in various industries, with considerable applications in Music & Video, Musicians, and DJs. Its unique properties make it an ideal choice for products that require durability, flexibility, and reliable performance. In this article, we will delve into the specifics of polyurethane coated webbing, exploring its benefits, applications, and why it is becoming increasingly popular.
What is Polyurethane Coated Webbing?
Polyurethane coated webbing consists of a high-strength webbing material that has been treated with a polyurethane coating. This process enhances the webbing's physical properties, providing a significant improvement in durability and resistance to environmental factors. The result is a material that is less prone to abrasion, UV degradation, and moisture absorption, making it suitable for a plethora of applications.
Benefits of Polyurethane Coated Webbing
The benefits of polyurethane coated webbing are extensive and varied:
- Durability: One of the primary advantages is its exceptional durability. The polyurethane coating offers resistance to wear and tear, which is crucial for products subject to heavy use.
- Weather Resistance: This type of webbing can withstand harsh weather conditions, making it suitable for outdoor applications.
- Flexibility: Unlike traditional materials, polyurethane coated webbing maintains its flexibility, allowing for a wide range of motion and usability.
- Lightweight: The material is both strong and lightweight, reducing the overall weight of the products, which is especially important in the music and entertainment industry.
- Customizability: Manufacturers can produce polyurethane coated webbing in various colors, patterns, and widths, allowing for tailored solutions for different needs.
Applications in the Music & Video Industry
In the realms of Music & Video, musicians, and DJs, polyurethane coated webbing is utilized in various innovative ways:
1. Equipment Straps
Musicians often require reliable straps for their instruments. Polyurethane coated webbing is used to create guitar straps, microphone straps, and equipment belts that provide both comfort and security. The robust coating ensures that these straps can endure the rigors of performance while remaining lightweight for ease of use.
2. Carrying Cases
Protecting sensitive equipment is paramount for musicians and DJs. Cases made with polyurethane coated webbing offer enhanced durability and weather resistance, which helps safeguard expensive gear against damage from moisture and impacts.
3. Speaker and Cable Management
For DJs, managing speakers and cables efficiently is crucial for smooth performances. Using polyurethane coated webbing to create robust cable ties and speaker straps helps keep everything organized, reducing the risk of tangled wiring that could cause accidents during a show.
4. Stage Fabrics
Polyurethane coated webbing can also be found in stage backdrops and rigging accessories. Its durability against wear and weather conditions ensures that visual elements remain intact and vibrant throughout performances.
How Polyurethane Coated Webbing Enhances Product Lifespan
One of the main concerns for manufacturers in any industry is the lifespan of their products. The inclusion of polyurethane coated webbing significantly enhances product longevity:
- Resistance to UV Rays: Unlike many conventional materials, polyurethane coated webbing does not degrade quickly when exposed to sunlight, making it perfect for outdoor uses, such as outdoor concerts and festivals.
- Moisture Management: The waterproof nature of polyurethane coatings ensures that products do not absorb water, thus preventing mold growth and material degradation.
- Anti-Abrasion Qualities: The coating protects the webbing from abrasions, increasing its usability in high-friction environments.
Manufacturing Considerations
Producing polyurethane coated webbing involves several manufacturing steps that ensure high-quality outcomes:
1. Material Selection
The base webbing material is chosen for its strength and flexibility. Common materials include nylon and polyester, both of which offer excellent tensile strength.
2. Coating Process
The application of the polyurethane coating must be conducted in controlled environments to ensure an even distribution and correct adhesion to the webbing.
3. Quality Testing
After production, rigorous testing should be performed to assess the tensile strength, flexibility, abrasion resistance, and overall durability of the finished webbing.
Safety and Compliance Standards
Industry standards for safety cannot be overlooked in the manufacture of polyurethane coated webbing. Ensuring compliance with health and safety regulations is vital:
- Material Certifications: Ensuring that all materials used in the production process are certified safe and meet industry standards is essential for gaining consumer trust.
- Testing for Toxicity: It is important to conduct toxicology tests on polyurethane coatings to ensure that they do not emit harmful substances.
- Environmental Considerations: The production process must also consider the environmental impact of both the webbing and the polyurethane coating.
Future Trends in Polyurethane Coated Webbing
The future of polyurethane coated webbing looks promising with advancements in material science and technology. Here are some trends to watch:
- Eco-friendly Innovations: With growing concerns about sustainability, manufacturers are exploring biodegradable lubricants and alternative materials that can enhance the webbing's environmental impact.
- Smart Fabric Integrations: The incorporation of smart technology into webbing for capabilities such as tracking and monitoring will become a focus area, especially in applications related to personal safety.
- Increased Customization: As demand grows for personalized products, the ability to custom-design polyurethane coated webbing will be vital for both consumers and businesses.
Conclusion
In summary, the rise of polyurethane coated webbing marks a significant advancement in material technology with vast applications in the Music & Video industry, especially among musicians and DJs. Its exceptional durability, flexibility, and weather resistance provide a competitive advantage in various products, ensuring they last longer while performing reliably. As industries continue to evolve, so too will the innovations surrounding this versatile material, promising a dynamic future in product manufacturing.
To learn more about the application of polyurethane coated webbing and how it can benefit your products, explore our catalog at enthun.com.