The Essential Guide to CNC Lathing Parts in Metal Fabrication
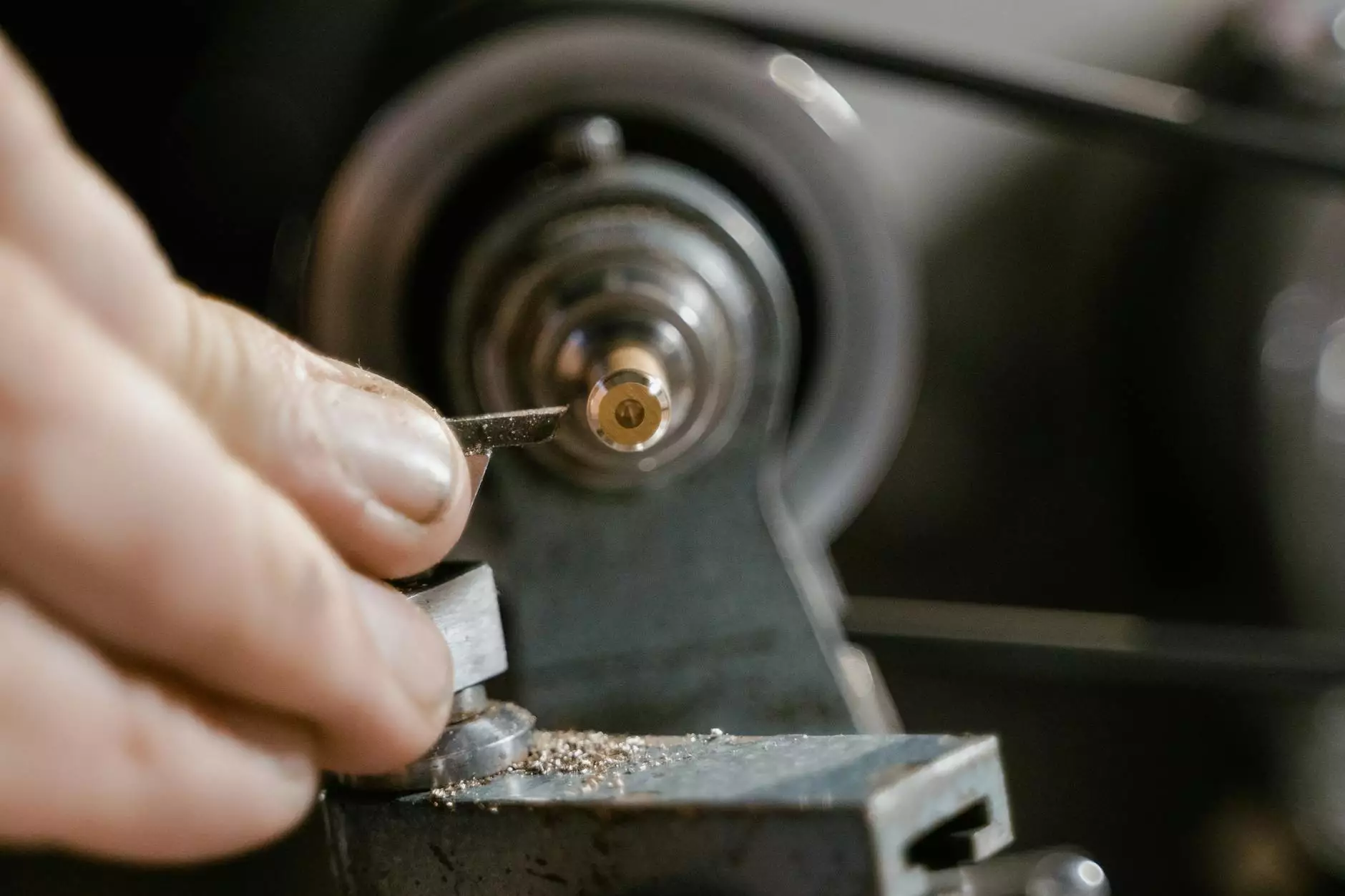
In the modern manufacturing landscape, CNC lathing parts play an increasingly vital role. As businesses strive for precision, efficiency, and cost-effectiveness, understanding the intricacies of these components can be a game-changer. At Deep Mould, a leader in the sector of Metal Fabricators, we dive deep into the world of CNC lathing parts, shedding light on their significance and benefits.
What are CNC Lathing Parts?
CNC (Computer Numerical Control) lathing refers to the process in which materials, predominantly metals, are shaped and cut using a computer-controlled lathe machine. This advanced technology allows for high precision and repeatability in creating cnc lathing parts that meet specific design requirements.
CNC lathing parts can range from simple components to intricate designs used in various industries, including automotive, aerospace, medical, and electronics. The ability to automate the lathing process has transformed traditional manufacturing, enhancing productivity and minimizing human error.
Applications of CNC Lathing Parts
The applications of cnc lathing parts are vast, given their versatility. Here are some of the primary areas where they find extensive use:
- Automotive Industry: CNC lathing parts are used in producing engine components, transmission parts, and various fixtures.
- Aerospace: Precision parts like turbine blades and landing gear components are manufactured using CNC processes.
- Medical Devices: Components for surgical instruments and diagnostic equipment are produced with stringent tolerances.
- Electronics: Housing and internal components of electronic devices frequently utilize CNC lathing for precision engineering.
- Overall Manufacturing: Nearly all sectors benefit from the precision and efficiency that CNC lathing can provide.
Advantages of Using CNC Lathing Parts
The choice to employ CNC lathing for producing parts is not merely a trend; it comes with an array of advantages that position it as a preferred method in modern manufacturing. Here are some of the key benefits:
- Precision and Accuracy: CNC machines can achieve tolerances that are often less than a thousandth of an inch, ensuring that parts fit together perfectly.
- High Efficiency: The ability to run multiple machines and automate processes leads to shorter production times and greater output.
- Repeatability: Once a design is programmed into a CNC machine, it can reproduce the same part multiple times with little variation.
- Complex Geometries: CNC lathing can produce intricate shapes that may be difficult or impossible to achieve using traditional machining methods.
- Reduced Waste: CNC lathing optimizes material usage, leading to less scrap and reduced costs.
- Flexibility: Changing designs requires minimal adjustments in CNC programming, allowing for quick changes in production.
Key Materials for CNC Lathing Parts
Understanding the materials used in the cnc lathing parts process is crucial, as different materials have unique properties that affect the machining process and the final product. Some commonly used materials include:
- Aluminum: Lightweight and strong, aluminum is easy to machine and offers good corrosion resistance.
- Steel: Known for its durability, steel is often used for parts requiring strength and toughness.
- Brass: With excellent machinability, brass is frequently used in applications requiring low friction.
- Plastic: Materials like nylon and acrylic are also utilized, particularly for non-metal applications.
- Composite Materials: Advanced composites are becoming increasingly popular for specialized applications.
The CNC Lathing Process Explained
The CNC lathing process typically involves several steps, ensuring that each component is finely crafted to meet exact specifications:
1. Design and CAD Modeling
The process begins with a detailed design, often created using CAD (Computer-Aided Design) software. This design is crucial as it serves as the blueprint for the CNC machine.
2. CAD to CAM Conversion
Once the design is finalized, it is converted into a CAM (Computer-Aided Manufacturing) file. This file contains the instructions that guide the CNC machine during the cutting process.
3. Material Selection and Setup
The appropriate material is selected based on the design requirements. The CNC machine is then set up with this material, ensuring everything is secure and properly aligned.
4. Machining Process
The CNC machine begins the machining process, carefully following the programmed instructions. This involves the rotation of the material and the movement of the tooling to remove material and create the desired shape.
5. Finishing
After the initial machining, parts may require finishing processes such as sanding, polishing, or coating to meet quality standards and enhance appearance.
Quality Control in CNC Lathing Parts Production
Quality control is fundamental in the production of cnc lathing parts. Various methods are employed to ensure that every component meets the strict standards necessary for its application.
Common practices include:
- Dimensional Inspection: Using precision measuring tools to verify that parts conform to specifications.
- Material Testing: Ensuring that the material used meets required properties for performance.
- Process Audits: Regularly reviewing processes to identify and mitigate potential errors.
Future Trends in CNC Lathing Technology
As manufacturing technology continues to evolve, several trends are shaping the future of CNC lathing:
- Automation: Increased automation and integration of IoT (Internet of Things) technologies are streamlining processes further.
- Advanced Materials: Research into new materials is driving innovation in part production.
- Sustainability Practices: There is a significant push towards more sustainable machining practices, focusing on reducing waste and energy consumption.
- AI Integration: Artificial intelligence is being utilized for predictive maintenance and optimizing machining parameters for better efficiency.
Choosing the Right CNC Lathing Services
When it comes to selecting a provider for cnc lathing parts, several factors should be considered for optimal results:
- Experience: Look for a company with extensive experience in your industry.
- Capabilities: Ensure they have the equipment and expertise to meet your specific needs.
- Quality Standards: Check their quality control practices and certifications.
- Customer Support: Strong customer service can make a significant difference, especially in communication and project management.
- Reviews and References: Seek feedback from previous clients to gauge reliability and performance.
Conclusion: The Importance of CNC Lathing Parts in Modern Manufacturing
In conclusion, cnc lathing parts are indispensable in the realm of metal fabrication, offering unparalleled precision, efficiency, and versatility. As industries evolve, the significance of these parts will only increase. For businesses looking to stay ahead of the curve, understanding and utilizing CNC lathing technology is essential.
At Deep Mould, we pride ourselves on our ability to deliver high-quality CNC lathing parts that meet the diverse needs of our clientele. Embrace the future of manufacturing and explore the potential of CNC technology in your operations today!